Consultancy Services
Consultancy Services -
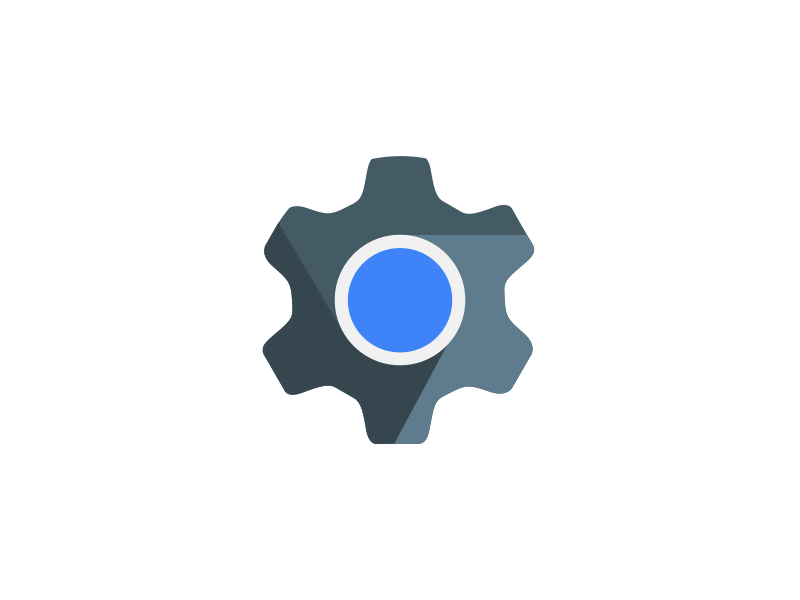
Organization restructuring
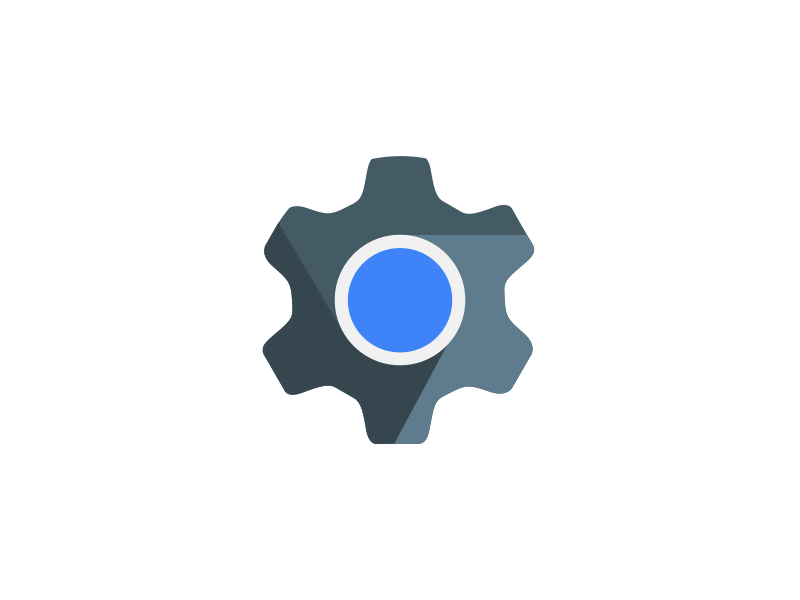
JD/DWM
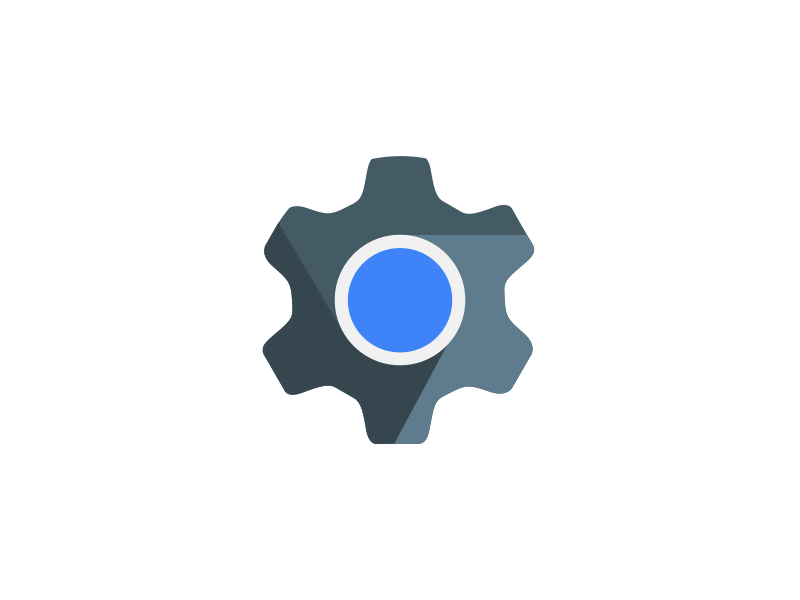
Recruitment
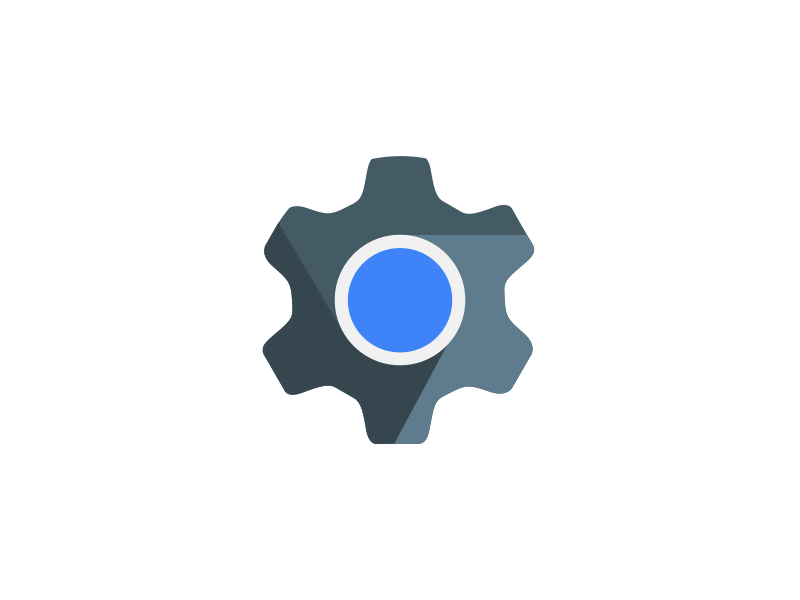
Team building
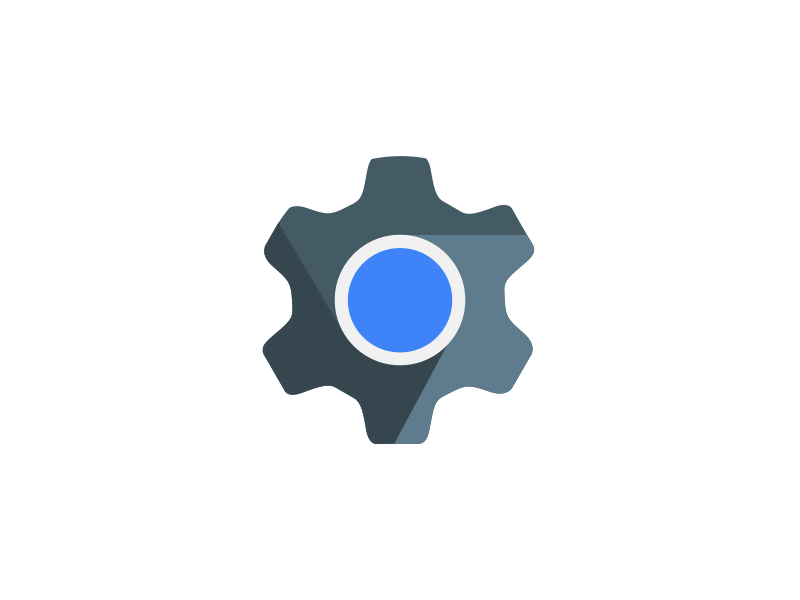
Company Goal sheet
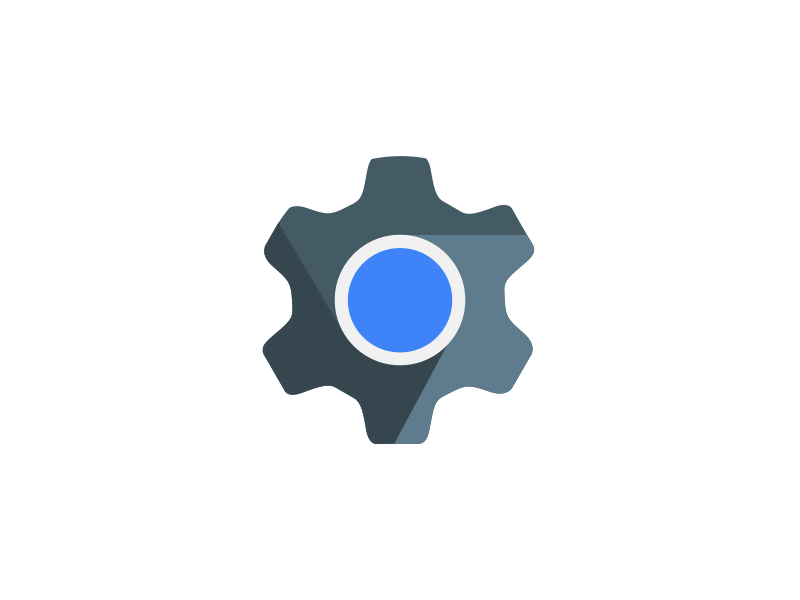
Dynamic Business planning
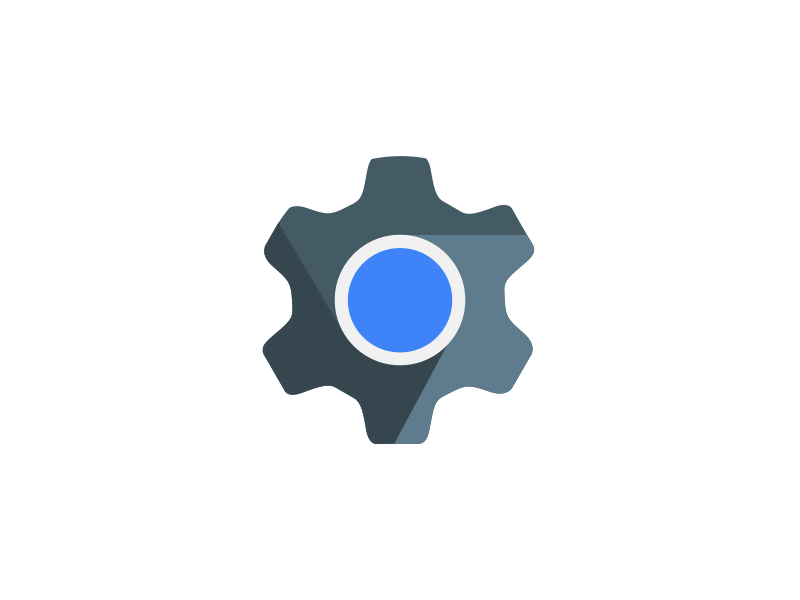
Vision /Missions/SWOT
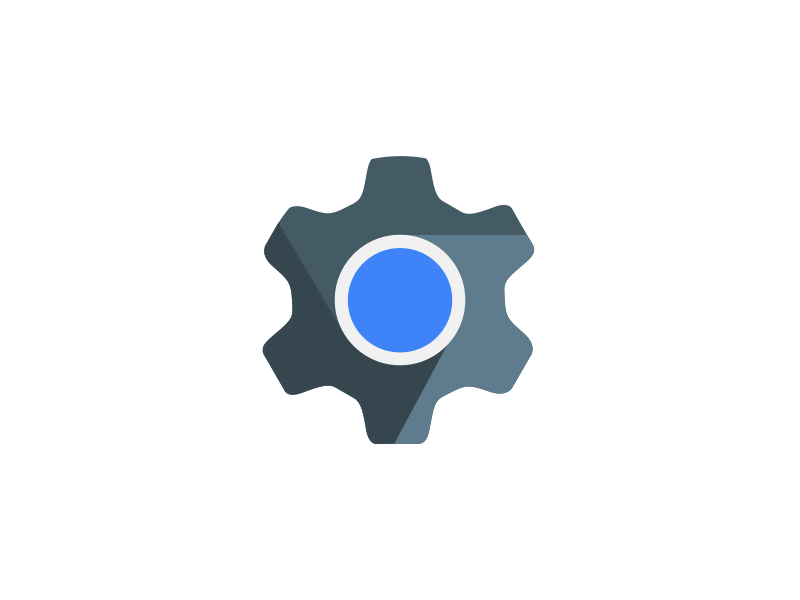
Quality improvement
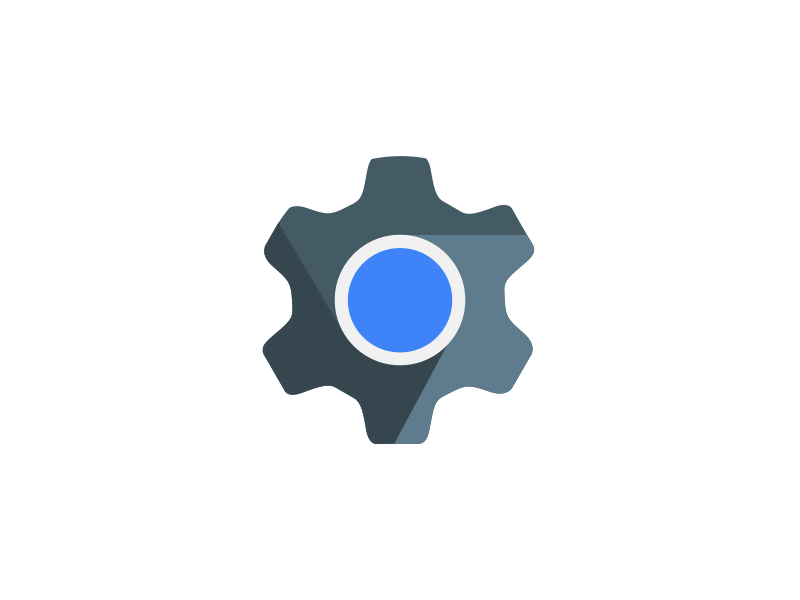
Productivity improvement
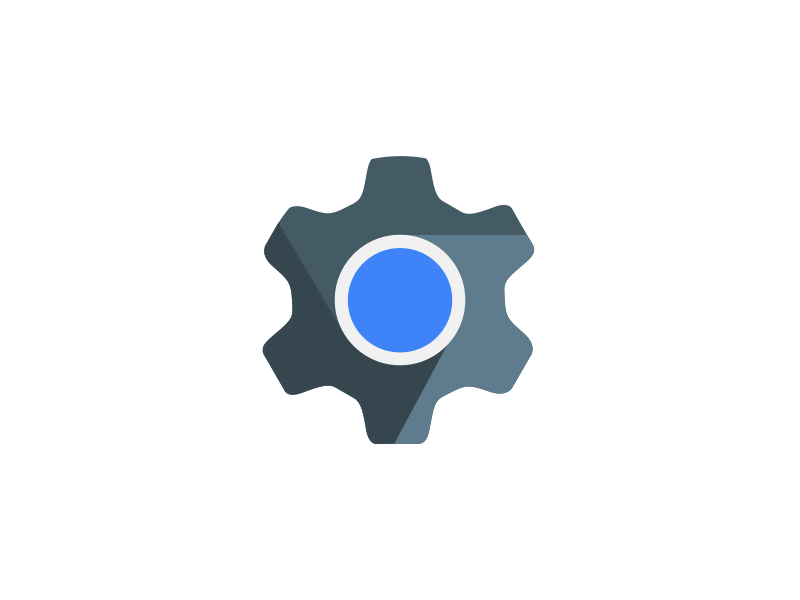
HR policies / Best Practices
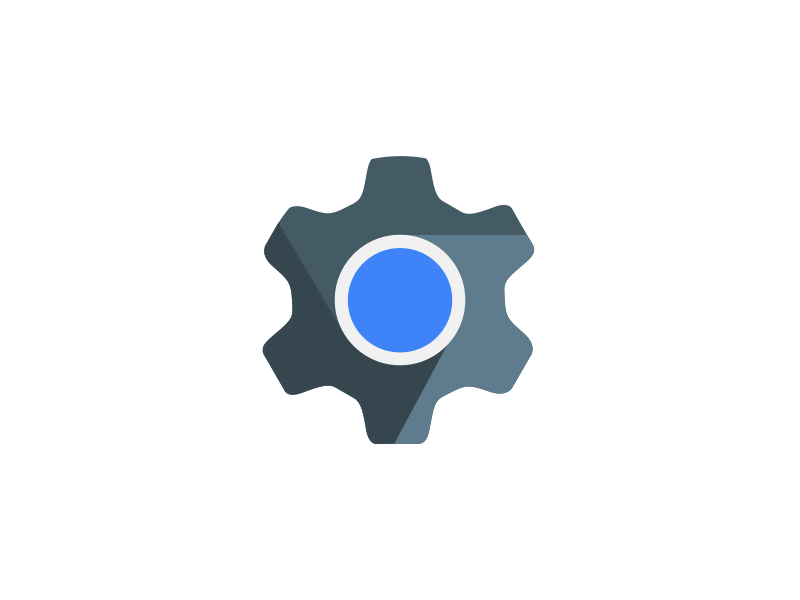
MIS
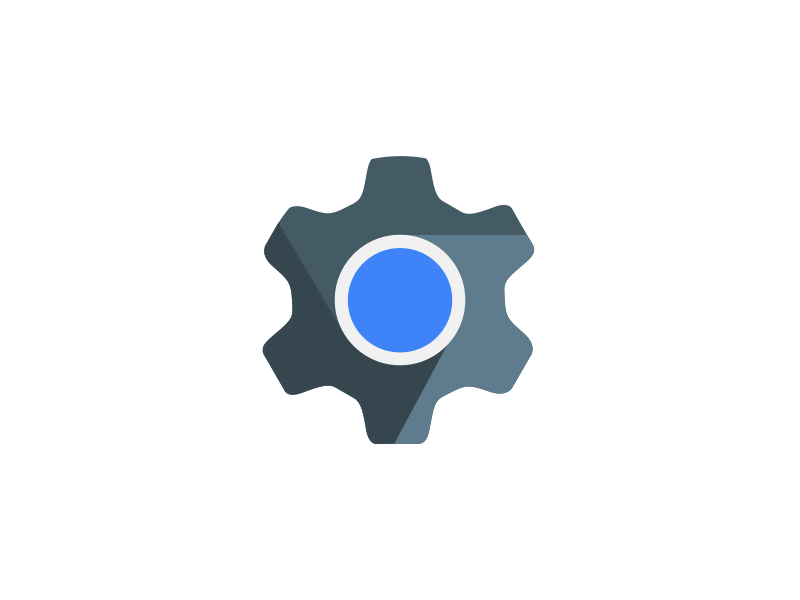
Overall Review Mechanism
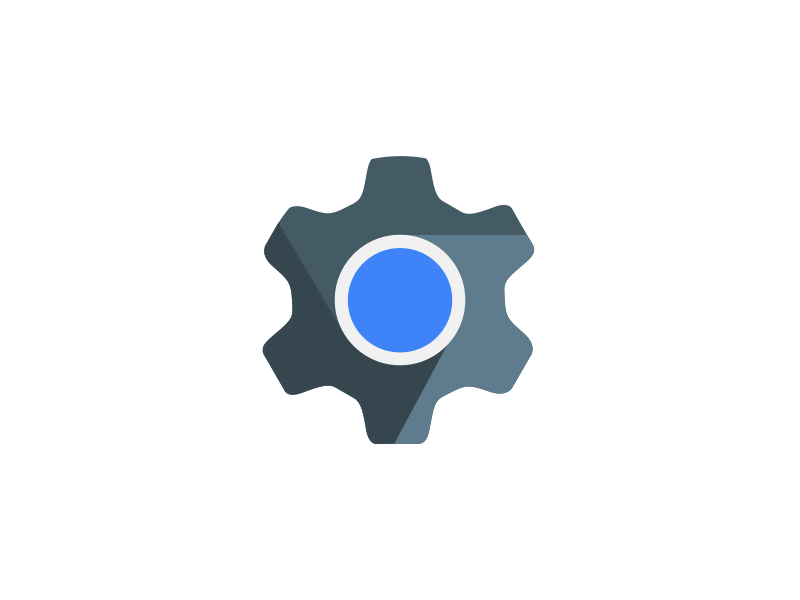
Commercial Discipline
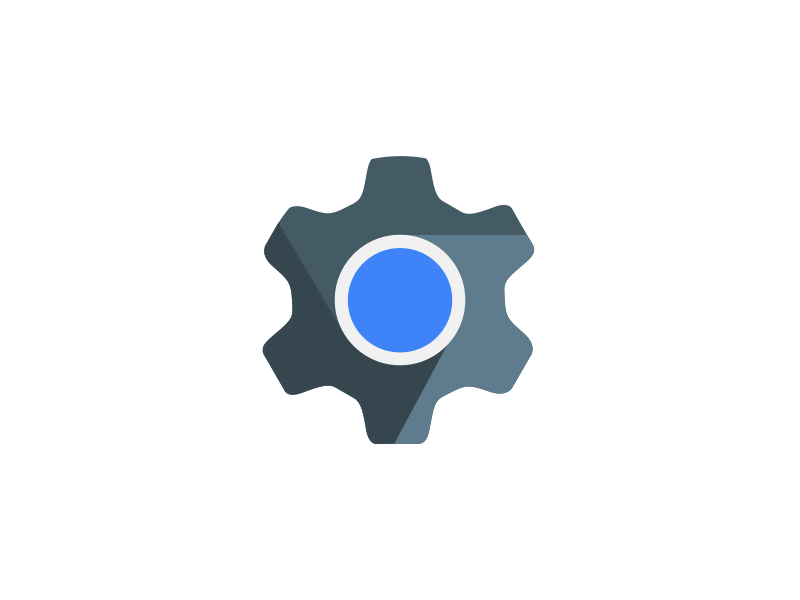
Commercial reviews
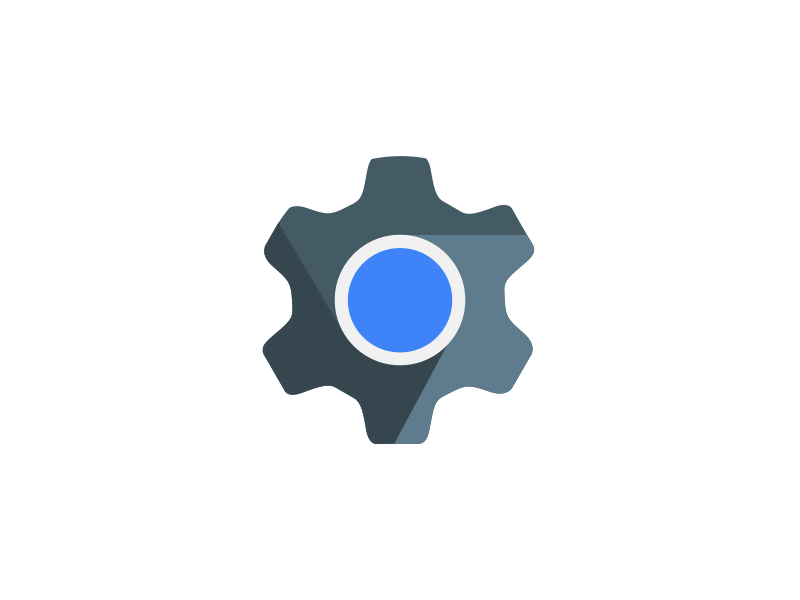
Performance Management System
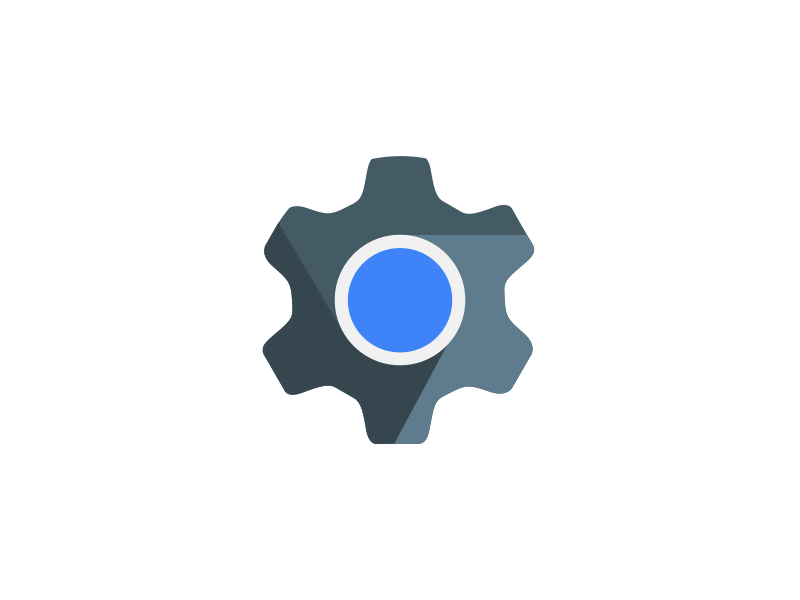
All types of effective Audits
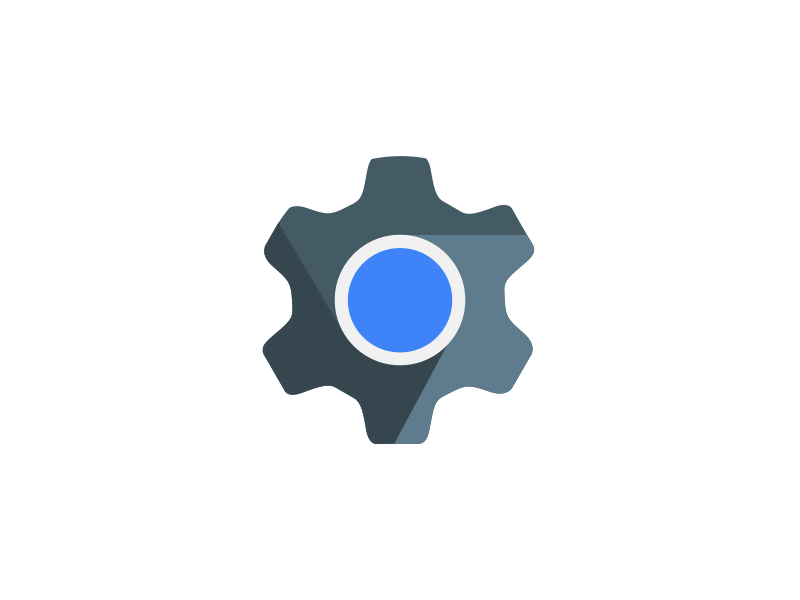
SOP management
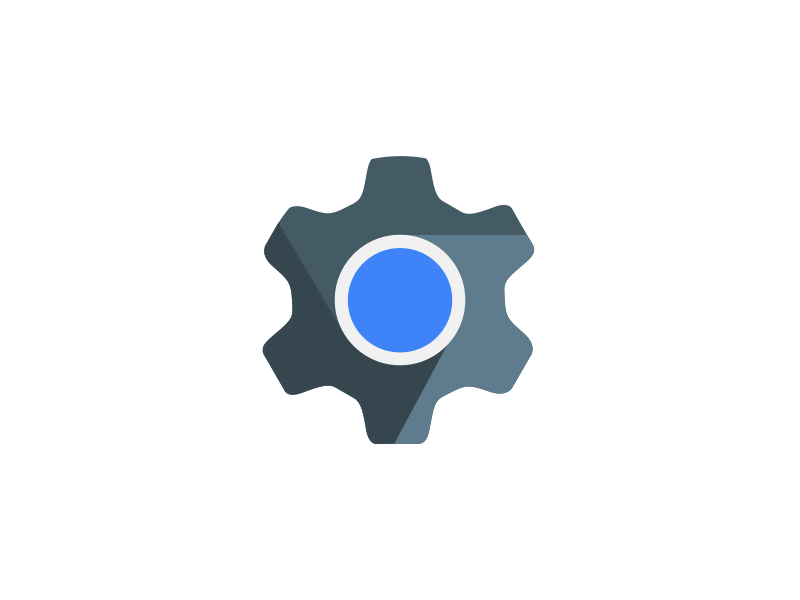
Lean Manufacturing /Manufacturing Excellency
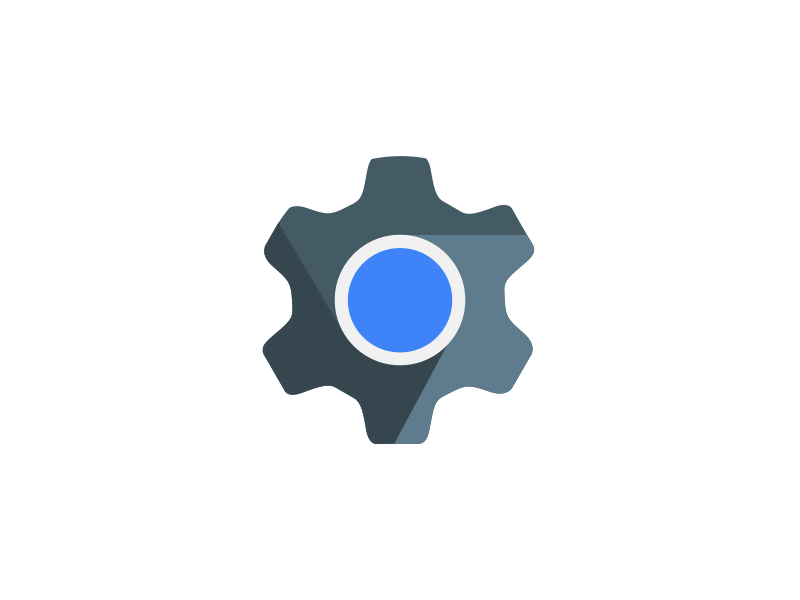
QMS/EHS/OHSAS certifications
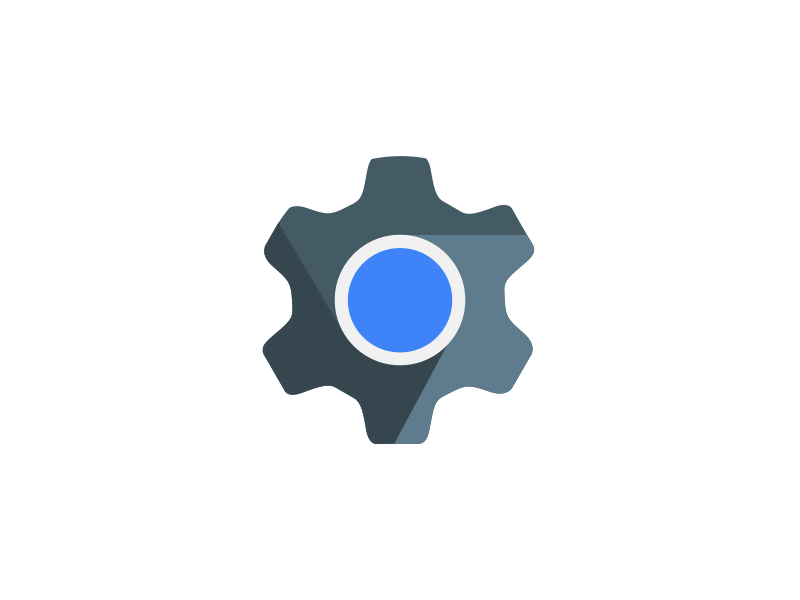
Key indicators setting
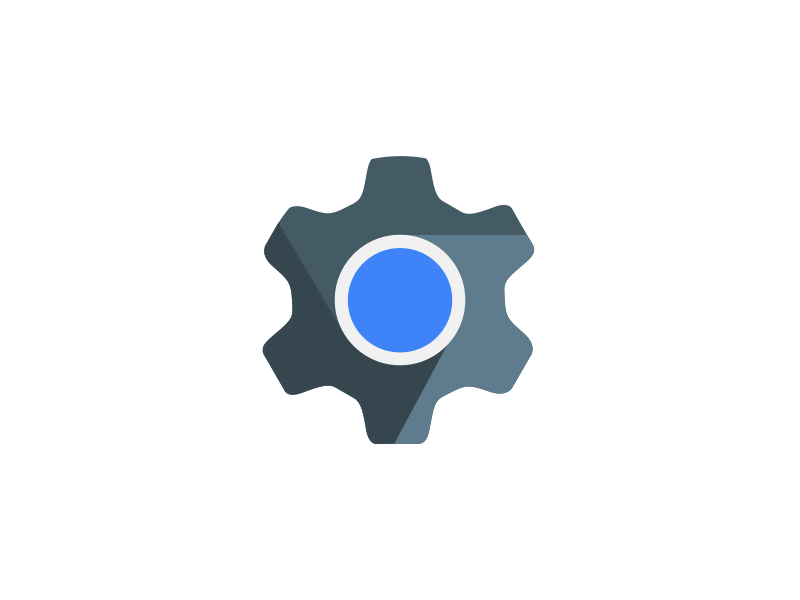
Management Dash Board
The Overall Excellence Journey At A Glance
Main Activities | Sub Activities | Benefits |
ABP (Annual Business plan) | Getting Inputs on ABP | See the whole business |
Preparation of SWOT | Strategic Focus | |
Expansion plan, Capex | Set priorities | |
Preparation of Business survey, Customer Analysis | Face Challenges, will able to work on our weakness & Threats | |
Creation of Vision / Mission/ Core Values statements | Develop accountability | |
Resource Management / Budgeting | Managing team members and tracking results will be easy | |
working of ROCE | Business objectives will be clear | |
Preparation of Final ABP in detail for current year & tentative of next 2 years | Realistic regular reminders to keep on track & Better Cash Flow | |
Organization chart & Recruitment | Detailed Discussion with Top Management about Requirements | Take Organization to Next Level |
Design proposed organization structure in-line with existing organization chart and company’s growth. | Efficient Decision Making | |
Finalize the same & sign off | Key Activities are not missed | |
Support in hiring activity as per revised organization chart | we can expect Clear Results | |
Verify whether the present team is capable of taking the organization at the next level. | Face Challenges | |
Job descriptions & DWM | Understand present working pattern | Job Clarity |
Interact with all Staff about their present activities pattern and what activities are missing to perform | very Less Gap Between Management Expectation & Actual | |
Drafting of JD & DWM | High moral of Employee | |
Check JD &DWM with Concern Staff/ HOD | Smooth Functions of all Depts. | |
Make changes and getting the JDs/ DWM signed off | No communication Gaps | |
PMS (for Middle & Senior Positions) | Prepared Company Goal Sheet | Clarity of Important Activities to be performed |
Visit organization last 2 years dept. wise performance | A Performance Management System enables a business to sustain profitability and performance by linking the employees’ pay to competency and contribution | |
Finalization of Company Goal sheet | High moral of Employee | |
Drafting KPI’s from company Goal for all HOD | Self-assessment is very simple | |
Discussing KPI with the CEO / Directors | Organizations can effectively manage the performance appraisal process with our online performance management system | |
Finalized KPIs to be discussed with each employee / HOD for smooth acceptance | it gives supervisors and subordinates an equal opportunity to express themselves under structured conditions | |
Sign off and implementing the same | It calls for a high level of co-ordination, channeled information flow, and timely review. | |
H.R. Policy | Framing the Customized H.R. Policy with all Rules & Regulations | provide rules and guidelines for decision-making in routine situations & its improve moral of all employees |
Review Current Gradation Pattern, if Required, Plan new Gradation system for all staff | provide a means of communicating information to new comer & Handling Employee Concerns are very easy. | |
Defining Must Be Requirements for organization | Good for training and Professional Development of all employees | |
Training to all Staff | Behavioral trainings | Improve Habits, Discipline, Soft Skills moral of all employees |
Lean Manufacturing / Mfg. Excellency | Training on 1 S & 2 S | Clean Factory |
Red Tag Campaign, Defining CFT | Each & Every resource is accountable | |
Gamba Rounds | safe working place | |
WPP /FPP | No searching no asking | |
3M Elimination- Training | Waste Elimination | |
Training on 3 S, 4S & 5S | Reduce Inventory | |
Training on TEI | Increase Productivity & Improve Quality | |
Training on my Machine | improves efficiency | |
Starting of Lean monthly MRM | Customer satisfaction | |
Key indicators | Training – Primary & Secondary Key Indicators | Review each and every area of business like Labour productivity, Inventory Tern Ratio, Delivery Schedule Adherence, Floor space utilization, cost of poor quality, Mean time to Repair & mean time between failure Etc. Etc., set targets for each and every area, improve them and finally improve overall profits. Improve Department wise co-ordination for good results. Improve Team work, Saving in energy biils and other overheads, Accountability in all resources |
Setting Reporting System for Top Management / Key indicators like LP/ITR/DSA/FSU/OEE/TEI/VAPCO/MTTR/MTBF/COPQ/FIFO/Electricity Bill Justification | ||
Check Department wise co-ordination, provide inter-locking, Define Formats for all technical Reviews. | ||
Start all Reviews | ||
Energy Conservation | ||
Material Accountability – Reconciliation of R.M. & B/o. Level 1 & 2 with Consumption of R.M. Justification. Training & Format Setting & Monitoring | ||
Quality Enhancement | Problem Solving tools /Poka yoke/ Kaizens -Training | Improve Customer Satisfaction, reduce Cost of poor Quality, Reduce Rework, Reduce Rejection, improve Quality level |
Training & Setting Customer Complaint/ Customer Return/Repeat Complaint & IHR Analysis by Parato Chart/ IHR/Cause & Effect Diagram /CAPA KRA. | ||
Audits | Set Dock Audits/ VDD Audits/ Process Audits/ Product Audits/ 5S Audit | Avoid wrong practices, proper accountability, improve Anti-theft culture |
Commercial Disciplined (MIS & Plant Performance Review) | Setting Commercial Team, their Formats | in the todays cost structure, it is important to have Commercial Disciplined to avoid loss |
Monitoring & Decisions on Stock statements/ Slow Moving / Non Moving | we can arrest loop hole immediately | |
Set Commercial Key indicators like – FFS/CF/Receivables/ Bad Debts/ Debtor Ageing/ Net Liability / C.C. Utilization trend/ Capex Analysis/ ROCE | Abnormal Expenses are immediately captured | |
Preparation of MIS | Cash flow managing becomes easy | |
Set Monthly Plant performance Review Meeting | improve profits | |
SOP Management | Defining the Key Processes | it helps for sustenance |
Preparation of SOP | Not person oriented | |
SOP Reviews | minimizing learning downtime | |
Finalization of SOP | Reduce errors and enhance productivity | |
Standardization of SOP with incorporation of last 3 years issues. | ensuring consistency in the performance of duties | |
SOP Bank | Multi Skilling becomes easy | |
Sustenance | Monitoring of overall Sustenance of Business Excellence Drive, close watch on MRM, Plant Performance Review, MIS, Gamba rounds Etc. And give inputs for further improvements. | whatever has been implemented will give us fruits only when is sustained, in normal scenario, sustenance is worried parts, therefore close monitoring becomes mandatory |